Tecnologia de impressão 3D para a construção – o banco Bloom
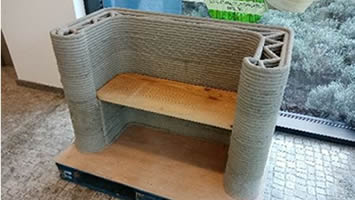
A par do desenvolvimento tecnológico nos diversos setores da indústria, a tecnologia de impressão 3D com materiais de base cimentícia para construção civil tem sido aplicada em diversos países. Têm sido executados diversos elementos para a construção, através de extrusão por equipamentos adaptados a um braço robótico ou um pórtico, permitindo construir em menos tempo, com menor custo e maior liberdade geométrica.
Exemplos desta técnica foram aplicados a mobiliário urbano e a edifícios. Em julho de 2020 foi executada a primeira casa com dois pavimentos em impressão 3D, situada na Bélgica e construída em 15 dias. Em tempo de pandemia, esta tecnologia foi utilizada na China para a execução de cápsulas de isolamento com 10 m² em apenas duas horas.
Entre os maiores desafios na impressão 3D está a adaptação entre o projeto, a máquina e o material. O projeto a ser executado deve passar pela programação que conduz o equipamento pelo trajeto pretendido, para que o material possa ser depositado com a forma adequada e resistência suficiente para que as sucessivas camadas possam ser aplicadas, dando forma à construção pretendida.
No presente estudo apresenta-se a construção de uma peça de mobiliário urbano, executado através de impressão 3D. Para o objetivo ser cumprido várias etapas foram percorridas, como a adequação de uma composição de argamassa adaptada ao equipamento de extrusão utilizado, e a elaboração dos códigos ajustados ao design pretendido para a definição do trajeto do robô que suportou a impressão.
Impressão 3D de material cimentício
A impressão 3D é uma tecnologia emergente e comummente ligada ao setor dos plásticos e da prototipagem, mas cada vez mais novas matérias-primas são feitas com esta tecnologia. O setor da construção tem cada vez mais razões para usar esta nova tecnologia pelas vantagens que oferece, como a redução drástica de desperdícios, a redução do erro humano e o facto de a construção poder ser otimizada de forma a ser feita durante 24h por dia, reduzindo significativamente os custos de produção e de mão-de-obra. Um dos mais recentes exemplos de aplicação desta nova tecnologia foi uma casa de dois andares impressa na Bélgica pela empresa Kamp C, concluída em apenas 15 dias e completamente feita in situ [1]. Outro exemplo são as câmaras de isolamento para quarentena produzidas em massa pela empresa chinesa WinSun, cada uma impressa em duas horas, segundo a empresa, fazendo uso de materiais reciclados no processo de fabrico [2].
No entanto, apesar de já haver diversos exemplos que demonstram a possibilidade de utilizar a tecnologia na construção, esta ainda carece de desenvolvimento para que seja possível usar todas as suas potencialidades. A utilização de matérias-primas sustentáveis, a modelação numérica do processo de impressão ou a incorporação de armadura durante na impressão 3D de material cimentício são exemplos que têm chamado a atenção da comunidade científica.
O Centro para o Desenvolvimento Rápido e Sustentado do Produto do Politécnico de Leiria tem, desde 2007, um forte foco na investigação e desenvolvimento no fabrico aditivo e desde 2017 tem apostado na impressão com material de base cimentícia em grande escala para a construção.
Tecnologia de impressão com materiais de base cimentícia
Materiais
Nos últimos anos tem-se verificado um aumento significativo na investigação e desenvolvimento na tecnologia de impressão 3D aplicada aos materiais de base cimentícia, e vários autores apresentaram resultados sobre a composição deste tipo de materiais.
Nesta linha, Rubio et al. [3] apresentaram bons resultados com proporções de ligante/agregado de 1:2 e 1:3 usando cinzas volantes e sílica de fumo e uma relação água/cimento de 0,5. Neste estudo foi também avaliada a possibilidade de incorporação fibras de polipropileno. Nos estudos realizados por Le et al. [4], a proporção ideal de agregado/ligante foi de 60/40, sendo que o ligante era constituído por 70% de cimento, 20% de cinzas volantes e 10% de sílica de fumo. A quantidade de superplastificante usado situou-se entre 0.5% a 1% do peso do ligante, e as fibras de polipropileno na proporção de 1,2 kg/m³. Kazemian et al. [5] usaram uma proporção de agregado/ligante de 70/30, estudando a influência da adição de 10% de sílica ativa, 1,18 kg/m³ de fibras, e 0,30% de nano argilas. O estudo constatou que a sílica e a nano argila aumentam a estabilidade da mistura, ao contrário do que acontece com as fibras de polipropileno.
Alguns autores têm procurado adicionar resíduos industriais na composição, aumentando a vertente ecológica do processo. Annappa et al. [6] demonstraram a viabilidade de incluir os resíduos do processo de transformação da pedra na composição de argamassa para impressão 3D. Os melhores resultados foram obtidos para uma composição com proporção cimento:pó de pedra de 2:1 e com adjuvante redutor de retração Sika Control 40. Ma et al. [7] apresentaram um estudo com a adição de resíduos de cobre da indústria mineira ao agregado natural, fixando a massa de agregado e adicionando cobre nas taxas de 10%, 20%, 30%, 40% e 50%. Os melhores resultados foram obtidos com o ligante composto 70% de cimento, 20% de cinzas volantes e 10% de sílica ativa, relação água/cimento de 0,26, 1,2 kg/m³ de fibras de polipropileno e 1,083% de superplastificante.
Para além de a composição ser importante para garantir o sucesso da impressão, é naturalmente necessário atender também à resistência após o endurecimento [8].
Equipamento de impressão
Na impressão 3D por extrusão com materiais de base cimentícia o processo é composto por 3 fases: mistura, bombeamento e impressão. A operação de impressão é realizada por um equipamento de extrusão associado a um sistema de posicionamento. Existem duas abordagens distintas mais comuns quanto ao sistema de posicionamento. Numa delas utiliza-se um pórtico cartesiano composto basicamente por vigas e pilares, como o BOD2, comercializado pela COBOD, onde os pilares suportam a estrutura e simultaneamente permitem a movimentação do eixo vertical (Z). As vigas, além de se moverem nos eixos Y e Z, suportam o equipamento de impressão e permitem o seu movimento no eixo X [9].
A alternativa a esta tecnologia é um braço robótico ou uma grua que suporta a cabeça de impressão. Um exemplo desta última foi desenvolvido pela empresa ApisCor: a grua é sustentada por um pilar central giratório (360°) fixado ao solo e com altura variável. No topo do pilar, é instalado um braço extensível horizontal que suporta a cabeça de impressão na extremidade. Uma das vantagens deste sistema é o seu formato compacto, que facilita o transporte [10].
Preparação do código para o robô
Para a impressão de uma peça com esta tecnologia é necessário efetuar, de forma mais ou menos sequencial, as seguintes tarefas: idealização e modelação, obtenção dos pontos, criação do ficheiro para o robô e otimização de parâmetros de impressão.
Na primeira fase, idealização e modelação, é fulcral identificar as limitações do equipamento a utilizar. Por exemplo, se o equipamento não permitir a impressão de geometrias com descontinuidades, que obrigariam à interrupção automática da extrusão do material, a peça deverá ser concebida como uma linha contínua e crescente.
A etapa seguinte consiste no processamento do modelo numa nuvem de pontos sequencial e contínua. O software divide o modelo sólido produzido em CAD 3D. O modelo é “fatiado” por planos que representam a altura de camada e os pontos das interseções são guardados, ou seja, o modelo é dividido por camadas planas perpendiculares ao eixo vertical, separadas pela altura de camada. Esta discretização é necessária devido à linguagem de programação utilizada pelo robô que, tal como no código G, apenas reconhece os pontos e executa as interpolações entre eles.
Com os pontos e os dados necessários à definição do programa, desde o nome, o plano de trabalho, a definição de ferramenta e velocidades, é gerado o ficheiro para o robô (Figura 1). Após a elaboração do programa, este é carregado no controlador do robô e procede-se aos testes iniciais. Estes testes são essenciais na verificação das trajetórias e na otimização dos parâmetros do processo de extrusão.
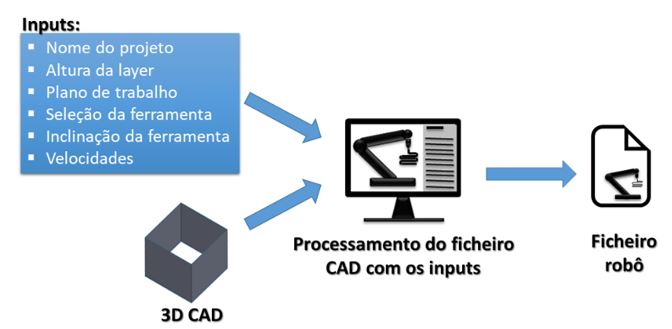
Figura 1. Mapeamento digital da preparação do código para impressão
O banco Bloom
Conceção
As tecnologias de impressão 3D têm sido uma ferramenta de apoio ao processo de desenvolvimento de produtos, tornando possível o fabrico com geometrias complexas e dando maior abrangência à criatividade na área do design.
Este estudo apresenta uma construção de mobiliário urbano realizada por impressão 3D (Figura 2), partindo dos mesmos princípios do design de produto. Esta peça tem como conceito ostentar um equilíbrio entre o jardim e o equipamento urbano, dando origem ao nome do objeto - Bloom.
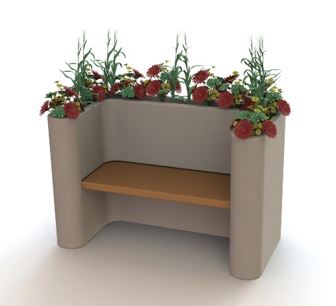
Figura 2. Modelo tridimensional do banco Bloom
Na preparação do código de impressão foi necessário atender às características da impressão 3D, bem como à necessidade de preparar um suporte para o assento em madeira e de reduzir o máximo possível o peso final da peça. Deste modo, o caso de estudo foi adaptado de forma que todas as camadas existentes na peça fossem de linha contínua, sem interrupções, e fossem colocadas com suporte da camada inferior. Para além disso, a estrutura foi concebida com paredes externas ao longo de todo o perímetro, interligadas por paredes interiores (Figura 3), para permitir a obtenção de uma peça suficientemente robusta e de peso bastante inferior ao que a solução maciça teria.
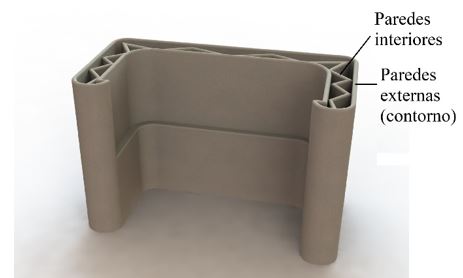
Figura 3. Modelo preparado para impressão
Neste sentido, o código foi elaborado de forma a que, entre a primeira camada e vigésima terceira camada, a trajetória fosse a que se apresenta na figura 4a), permitindo o suporte da tábua de madeira para o assento. Desde a vigésima quarta camada até à quadragésima oitava, a trajetória é a que se ilustra na figura 4b), permitindo o encaixe e fixação da placa de madeira, e a concretização do encosto.
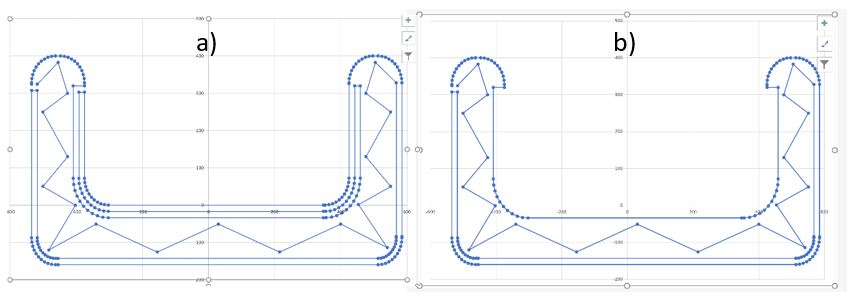
Figura 4. Geometria gerada pelo código de impressão
Materiais, equipamento e processo de impressão
A composição da mistura para a impressão 3D deve ser tal que permita a sua utilização pelo equipamento nas operações de mistura, bombagem e extrusão, bem como a construção do objeto pretendido. A reologia da pasta fresca é essencial em todo o processo. Na deposição, é necessário que a consistência da pasta confira adequada capacidade de suporte das camadas inferiores, aspeto que poderá limitar a altura do objeto a imprimir.
Neste sentido, foi desenvolvido um trabalho experimental com vista à obtenção de uma mistura que cumprisse estes requisitos, já publicado [11]. Foram utilizados dois tipos de agregados distintos, rocha calcária e rocha granítica, e, para ambos, dois tipos de granulometria, uma com dimensão máxima de 2 mm e outra com 1 mm. Utilizou-se cimento do tipo CEM II A/L 42.5 R, cinzas volantes, superplastificante Viscocrete e acelerador de presa MasterX-Seed 130. Foi avaliada a influência da proporção ligante/inerte, proporção cimento/cinzas, superplastificante e acelerador de presa nos resultados da impressão de uma peça com a geometria apresentada na Figura 5.
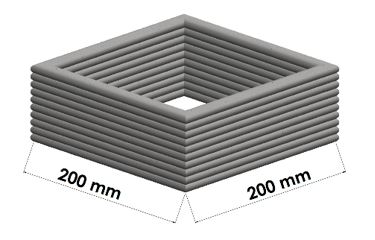
Figura 5. Geometria adotada nos ensaios de impressão para otimização da mistura
Os resultados obtidos nos testes de impressão foram avaliados através da qualidade da superfície pela observação de possíveis fissuras, deformações ou rotura das camadas no estado fresco. Esta avaliação foi comparada com as propriedades frescas e endurecidas da argamassa. Para tal, foram feitas misturas num misturador mecânico de acordo com as recomendações da norma EN 196-1 [12]. As propriedades medidas na pasta fresca foram a consistência (EN 1015-3 [13]) e o tempo de vida útil (EN 1015-9 [14]), como parâmetros de calibração para uma boa extrusão e impressão. A mistura com melhor desempenho é constituída por inerte de rocha calcária, com proporção ligante/inerte de 50/50% e proporção cimento/cinzas de 70/30% [11].
O equipamento utilizado consiste numa misturadora de 100 l que deposita a mistura pronta numa bomba que eleva o material cimentício através de uma mangueira até à cabeça de impressão, inserida braço robótico modelo Yaskawa Monto-man HP20F com carga útil de 20 kg, e com seis eixos de rotação. A cabeça de impressão, desenvolvida no CDRSP em colaboração com a empresa Periplast, é acionada através de um motor elétrico, possuindo a possibilidade de ajustar o caudal e um bico de extrusão de 20 mm de diâmetro (Figura 6).
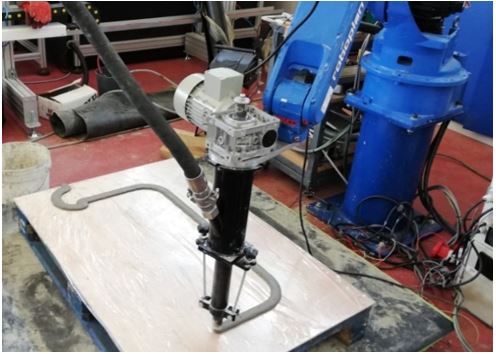
Figura 6. Equipamento de impressão
A velocidade adotada para a cabeça de impressão foi de 70 mm/s, com uma velocidade de rotação do motor de 50 Hz, de forma a obter um filamento com a geometria desejada. A largura de cada camada foi de 23 mm, com altura de 15 mm. Neste caso de estudo foram impressos 491 metros de filamento, correspondendo a cerca de 400 kg de material. O resultado final apresenta-se na Figura 7.
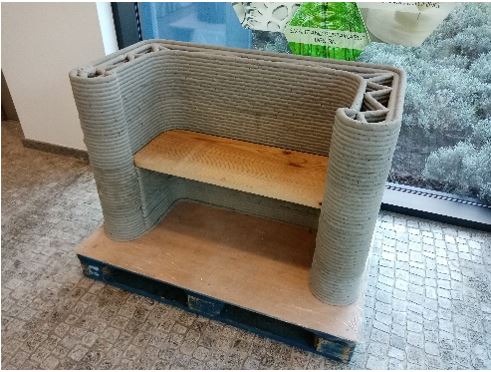
Figura 7. O banco Bloom impresso
Considerações finais
A tecnologia de impressão 3D tem sido usada em diversos exemplos na construção, nomeadamente por ser um processo rápido, com menor desperdício e que permite maior liberdade no design.
Esta tecnologia tem também chamado a atenção da comunidade científica, tendo-se assistido a um incremento significativo da investigação e desenvolvimento nesta área nos últimos anos. A reologia da pasta é determinante no processo de impressão, devendo ser ajustada ao equipamento e adequada à construção que se pretende imprimir.
No presente trabalho foi desenvolvida uma argamassa adequada ao equipamento de impressão, permitindo realizar as operações de bombagem, extrusão e de impressão do banco Bloom. O caso de estudo apresentado é o resultado do trabalho de uma equipa multidisciplinar, com conhecimentos distintos e orientados para a impressão da peça de mobiliário urbano.
Agradecimentos
Este trabalho foi financiado por fundos nacionais através da FCT - Fundação para a Ciência e a Tecnologia, I.P., no âmbito do projeto UID / Multi / 04044/2013 e pela Agência Nacional de Inovação através do projeto Add.Additive (add additive manufacturing to Portuguese industry – projeto número 24533).
Os autores agradecem os apoios das empresas LenaAgregados, pela disponibilização de materiais para impressão, e Periplast, no desenvolvimento da cabeça de impressão.
Referências
[1] KAMPC, 3D-printing in the construction world, (2020). https://www.kampc.be/c3po_eng (accessed October 1, 2020).
[2] GCR, Instant isolation rooms: Chinese firm prints quarantine pods for hospitals struggling with virus, (2020) Global Construction Review. https://www.globalconstructionreview.com/news/instant-isolation-rooms-chinese-firm-prints-quaran/ (accessed October 1, 2020).
[3] M. Rubio, M. Sonebi, S. Amziane, 3D Printing of Fibre Cement-Based Materials?: Fresh and Rheological Performances, in: M.S. Sofiane AMZIANE (Ed.), 2nd Int. Conf. Bio-Based Build. Mater., 2017: p. 10.
[4] T.T. Le, S.A. Austin, S. Lim, R.A. Buswell, R. Law, A.G.F. Gibb, T. Thorpe, Hardened properties of high-performance printing concrete, Cem. Concr. Res. 42 (2012) 558–566. doi:10.1016/j.cemconres.2011.12.003.
[5] A. Kazemian, X. Yuan, E. Cochran, B. Khoshnevis, Cementitious materials for construction-scale 3D printing: Laboratory testing of fresh printing mixture, Constr. Build. Mater. 145 (2017) 639–647. doi:10.1016/j.conbuildmat.2017.04.015.
[6] V. Annappa, F. Gaspar, A. Mateus, J. Vitorino, 3D Printing for Construction Using Stone Sludge, in: A. Rodrigues, H., Gaspar, F., Fernandes, P., Mateus (Ed.), Sustain. Autom. Smart Constr. Proc. Int. Conf. Autom. Innov. Constr. (CIAC-2019), Leir. Port., Springer International Publishing, 2019.
[7] G. Ma, Z. Li, L. Wang, Printable properties of cementitious material containing copper tailings for extrusion based 3D printing, Constr. Build. Mater. 162 (2018) 613–627. doi:10.1016/j.conbuildmat.2017.12.051.
[8] G. Ji, T. Ding, J. Xiao, S. Du, J. Li, Z. Duan, A 3D printed ready-mixed concrete power distribution substation: Materials and construction technology, Materials (Basel). 12 (2019). doi:10.3390/ma12091540.
[9] COBOD, MODULAR 3D CONSTRUCTION PRINTER, (2020). https://cobod.com/bod2/ (accessed October 1, 2020).
[10] C. Clarke, APIS COR 3D PRINTS A HOUSE IN ONE DAY, (2020). https://3dprintingindustry.com/news/apis-cor-3d-prints-house-one-day-106783/ (accessed October 1, 2020).
[11] F. Brun, F. Gaspar, A. Mateus, J. Vitorino, F. Diz, Experimental Study on 3D Printing of Concrete with Overhangs, in: S.T. Bos F., Lucas S., Wolfs R. (Ed.), Second RILEM Int. Conf. Concr. Digit. Fabr., DC 2020. RILEM Bookseries, vol 28. Springer, Cham., 2020. doi:10.1007/978-3-030-49916-7_77.
[12] EN 196-1 Methods of testing cement - Part 1: Determination of Strength, European Committee for Standardization, 2016.
[13] EN 1015-3 Methods of test for mortar for masonry - Part 3: Determination of consistence of fresh mortar (by flow table), European Committee for Standardization, 1999.
[14] EN 1015-9 Methods of test for mortar for masonry - Part 9: Determination of workable life and correction time of fresh mortar, European Committee for Standardization, 1999.
Em colaboração com Francis Brun, ESTG, Politécnico de Leiria, João Vitorino, CDRSP, Politécnico de Leiria, Liliana Gouveia, CDRSP, Politécnico de Leiria, Francisco Diz, CDRSP, Politécnico de Leiria, Ricardo Loureiro, CDRSP, Politécnico de Leiria, Rui Barbeiro, LenaAgregados, e Artur Mateus, ESTG, CDRSP, Politécnico de Leiria
Professor adjunto, Politécnico de Leiria
Se quiser colocar alguma questão, envie-me um email para info@construcaomagazine.pt
Outros artigos que lhe podem interessar